Battenberg pioneer of robotic measuring
Our mission in 1988 to replace special machines in the area of quality assurance with measurement robots led us to the invention of robotic measuring, with the aim of introducing transparent and comparable quality ratings in the automotive industry. Due to the high level of customer satisfaction, robotic measuring is now established and recognized in industry as a reference and benchmark for validatable quality ratings. Our principle of continuously developing robotic measuring through intensive, trusting customer relationships has led to new, effective and efficient applications. With reliability and continuity, we develop sustainable innovations that lead to further unique selling points for Battenberg Robotic. With RobSimulation for virtual simulations and mobile autonomous measurement robots, we offer new strategies for indoor/outdoor quality assurance.
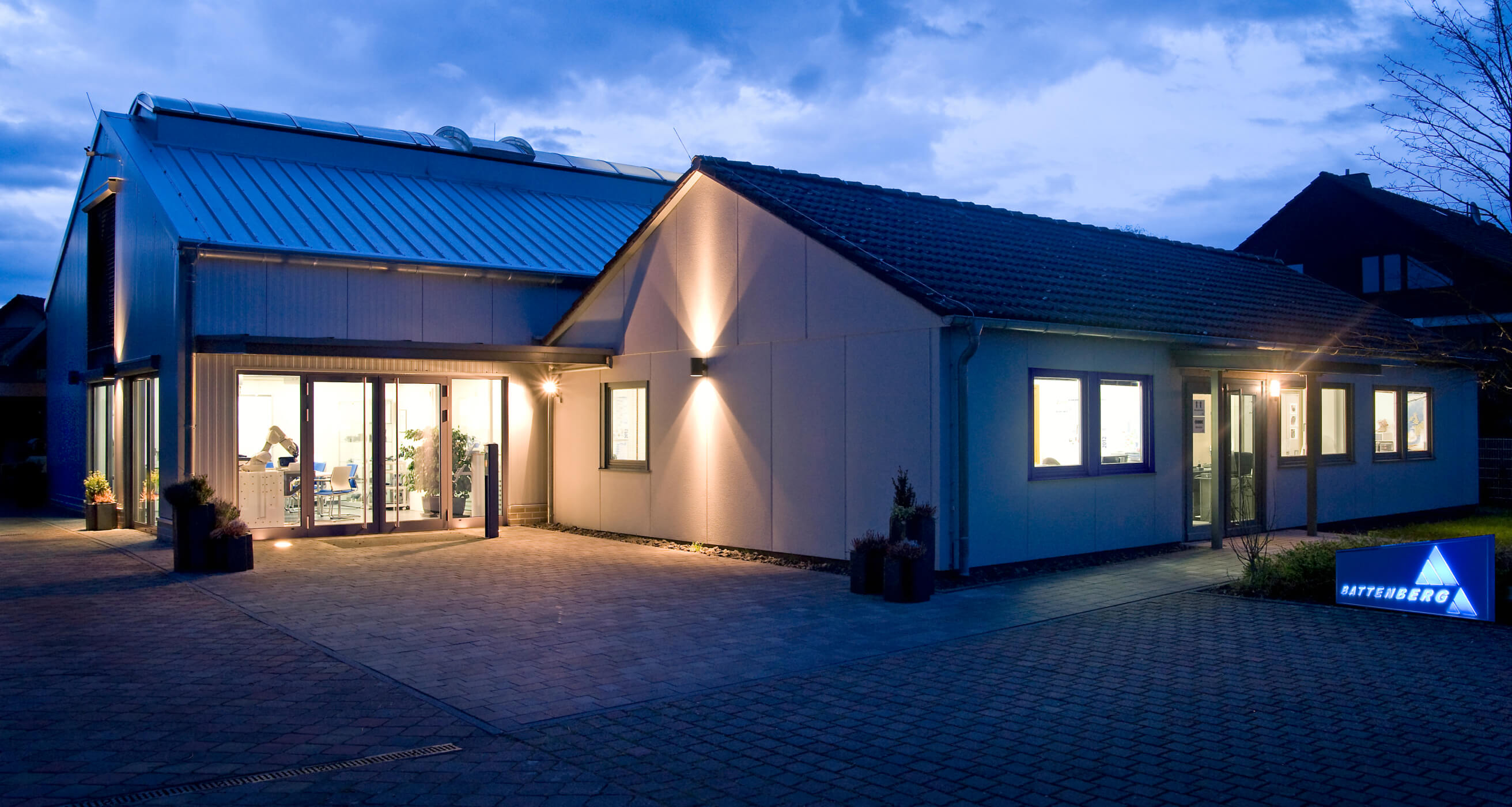
Our mission and vision
We want to develop cognitive systems for efficient development and flexible manufacturing in order to be able to produce product quality in line with human expectations.
Development and testing processes are simulated early on using CAD data, FunctionalTwins and self-learning algorithms and then transferred to real systems for virtual commissioning.
For an improved quality assessment, test results should be made available more quickly and transparently in a data ecosystem.
With a focus on sustainability and resource efficiency, we want to use virtual simulations to reduce the number of prototypes and achieve high competitive advantages for our customers.
We develop cognitive measuring robots.
- Robotic measuring is now the standard and reference for validatable quality assessment throughout the supply chain.
- Integration of a data ecosystem for faster availability of test results to assess quality at an early stage.
- Focus on sustainability and resource efficiency through predictive planning using simulation.
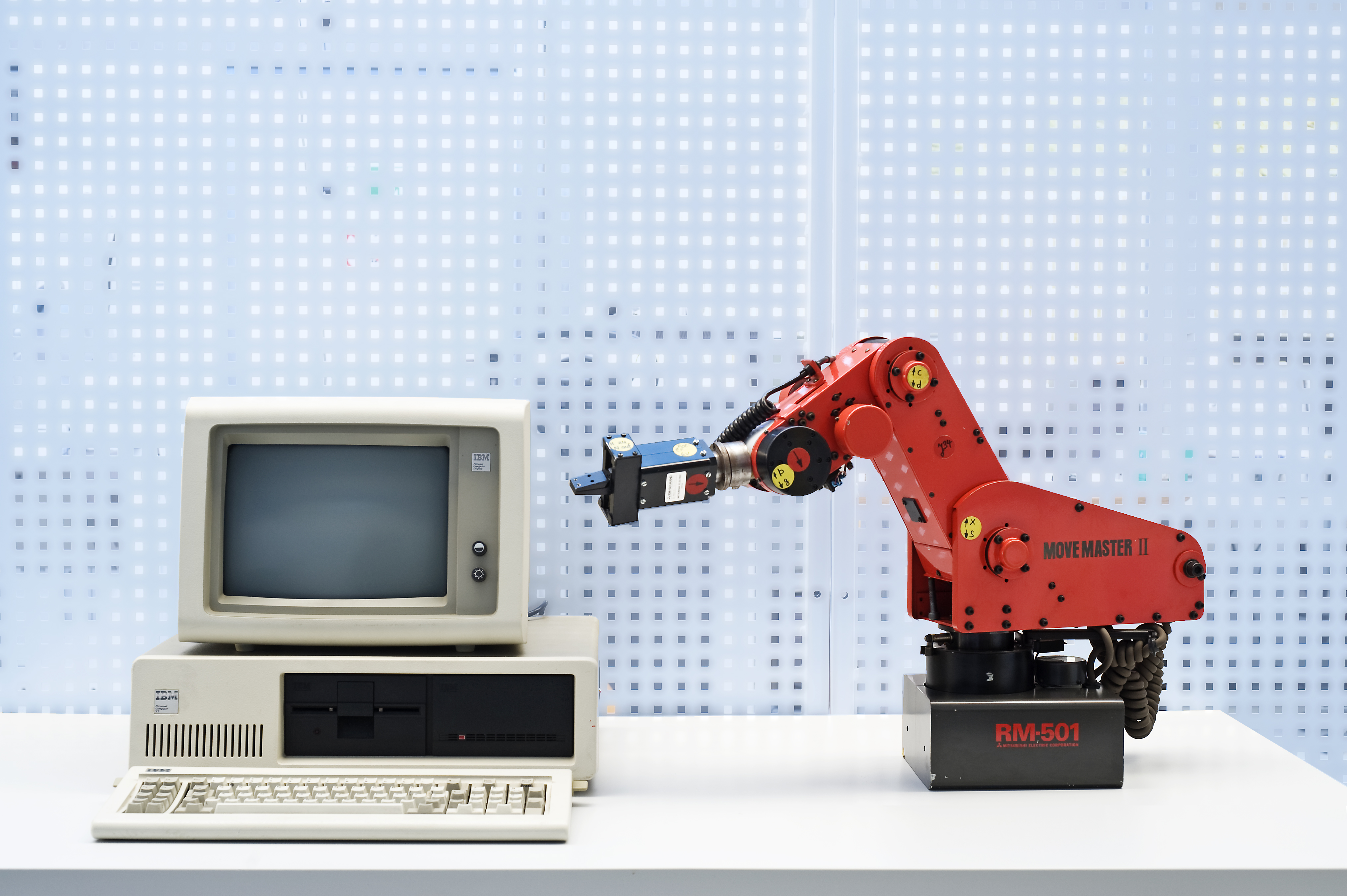
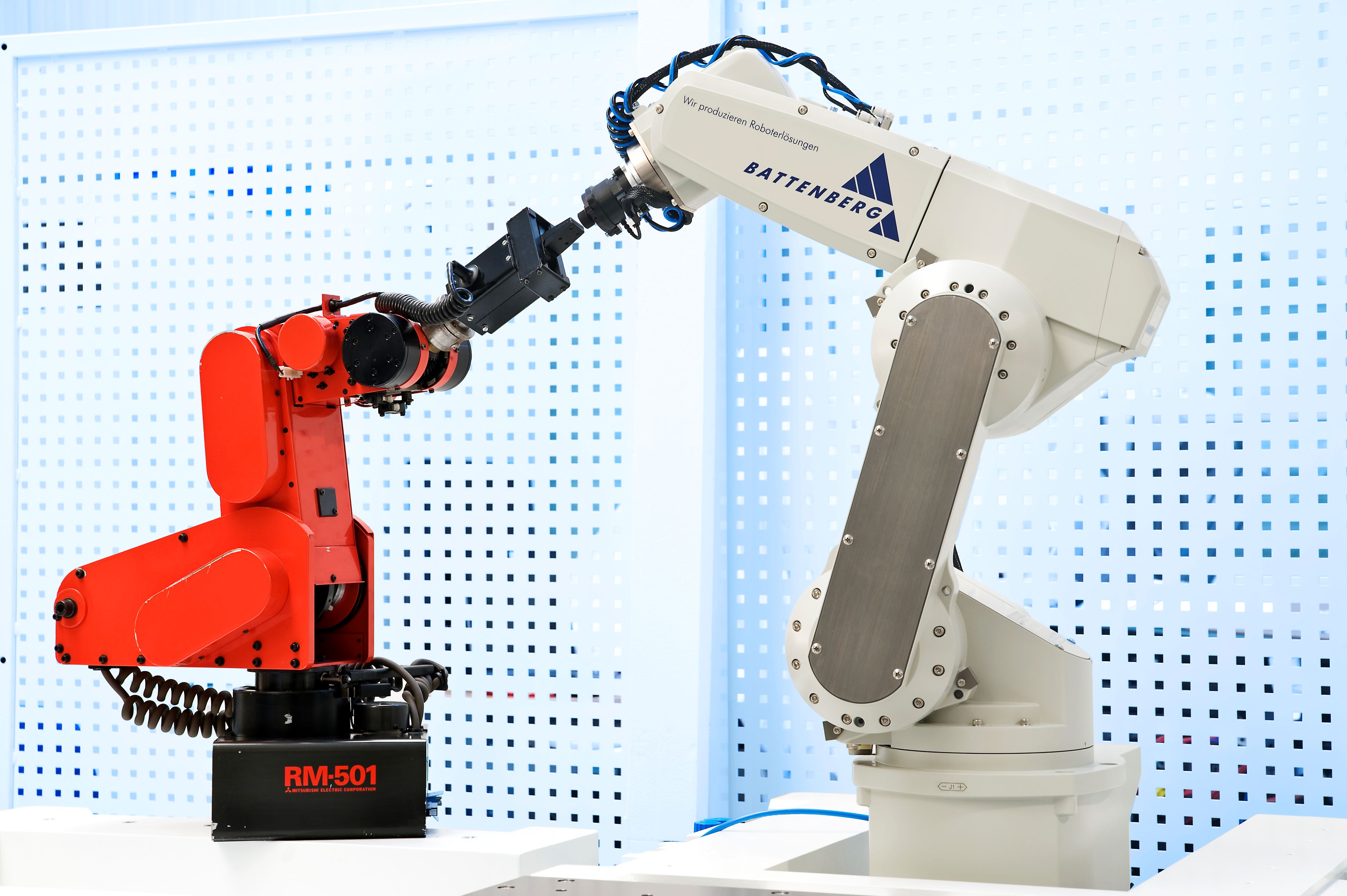
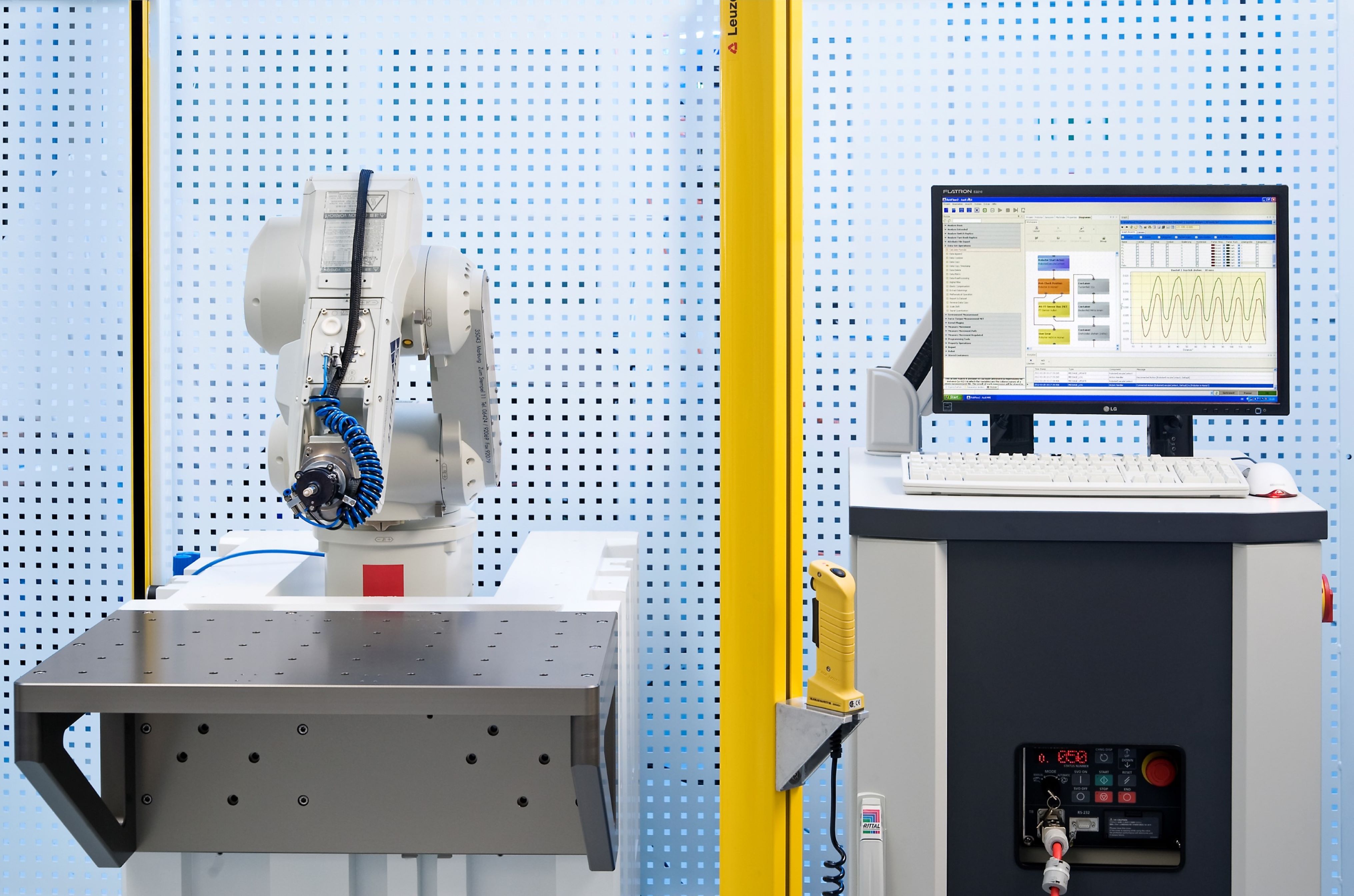
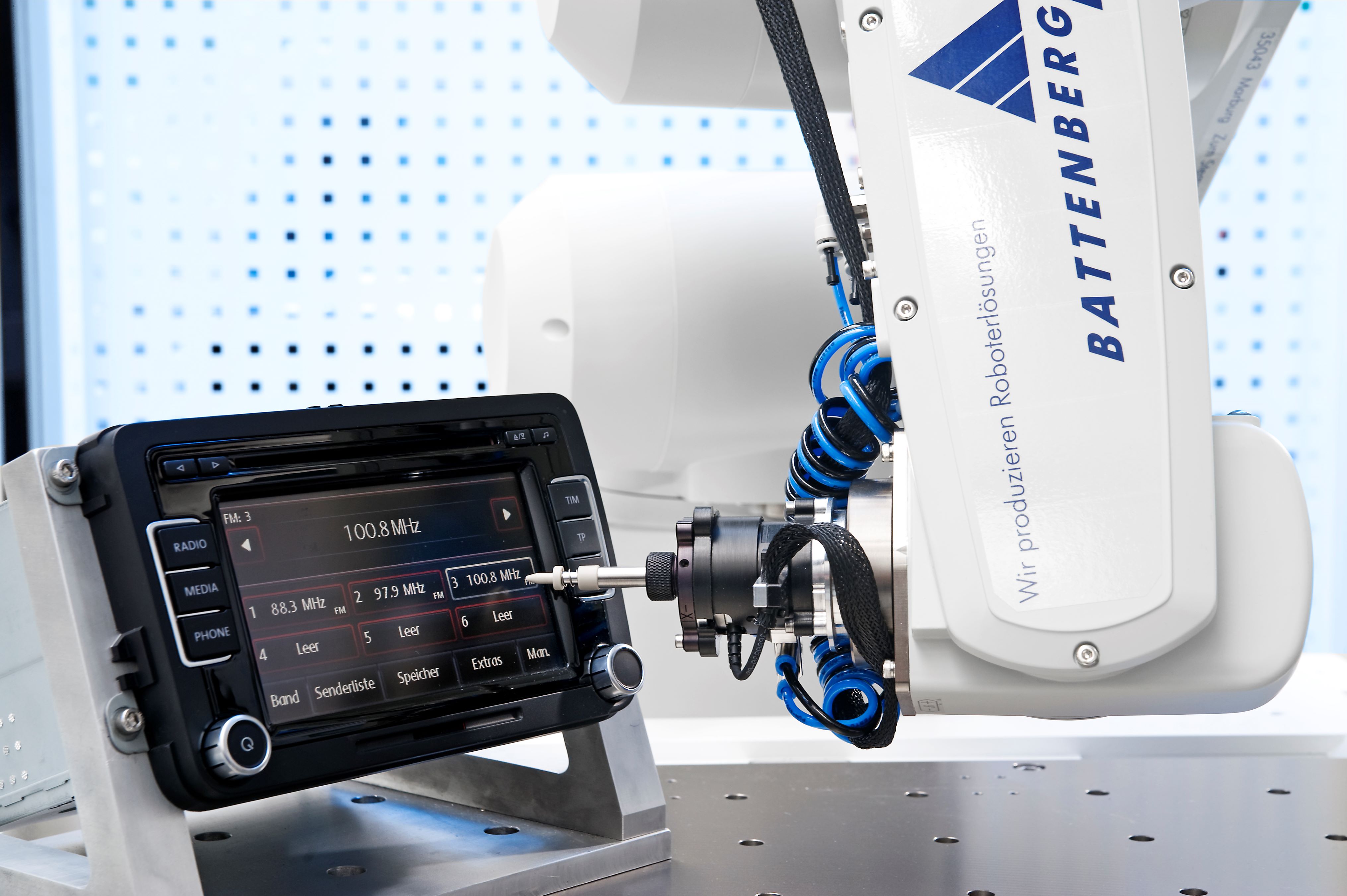
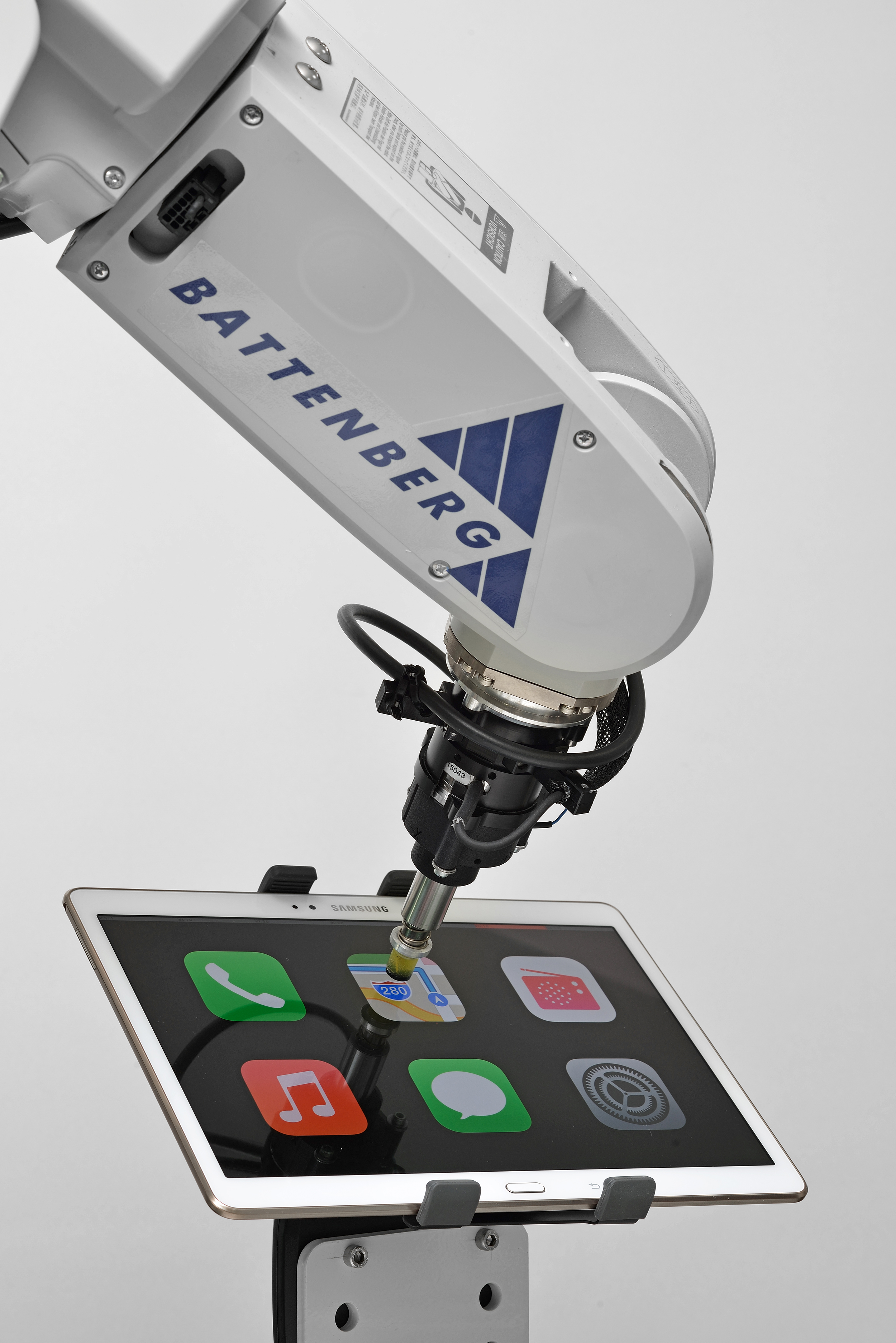
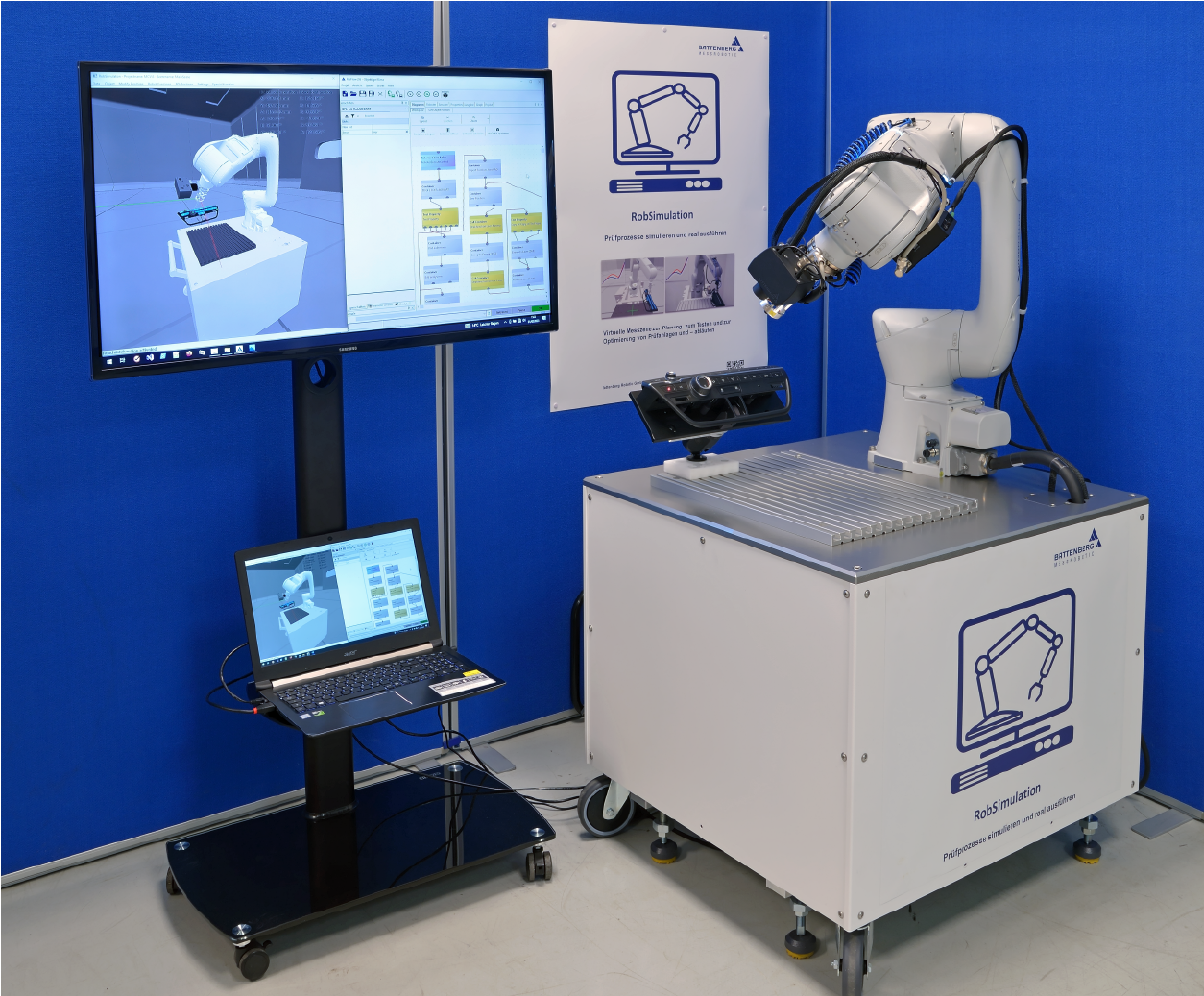
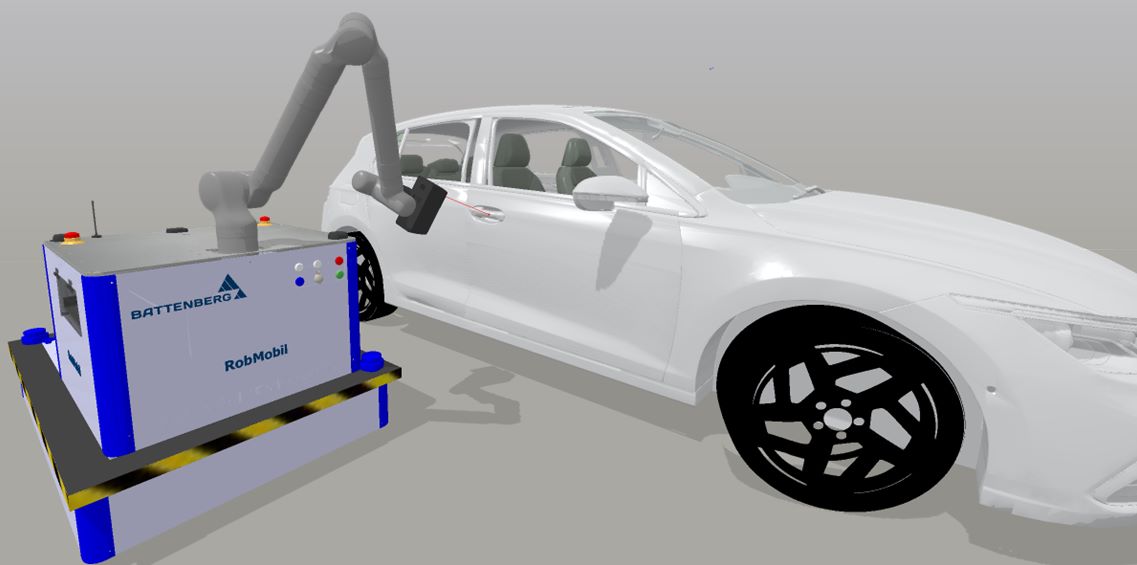
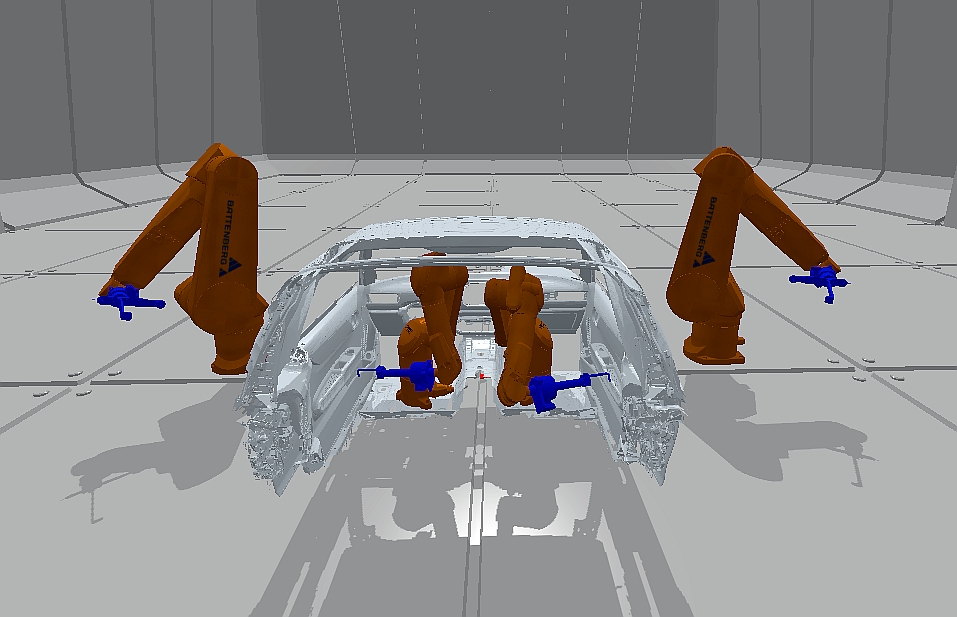
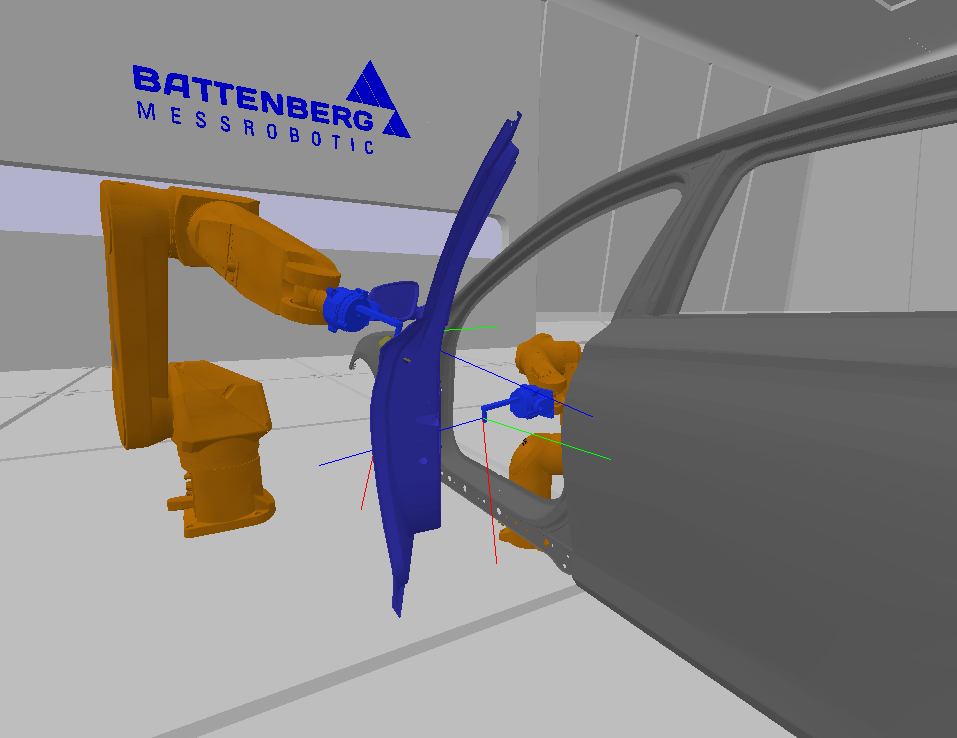
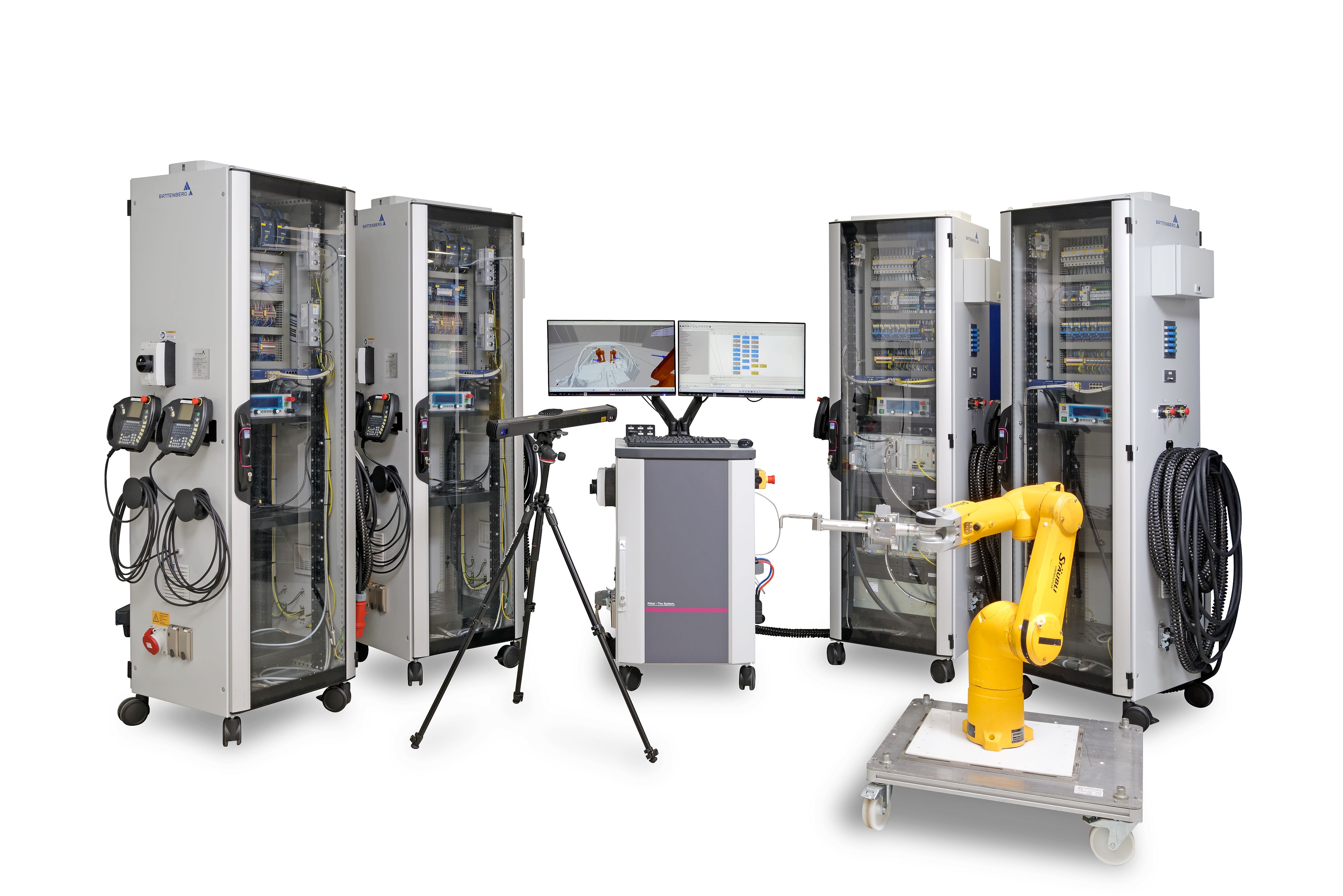

History of Battenberg
- Founding of the company “Battenberg Applied Computer Technology” by Günther Battenberg
- Moving into the current company headquarters in Marburg
- Development of mobile data acquisition systems in vehicles
- Development of haptic test systems for interior components
- Market launch of robotic measuring with Mitsubishi robots for haptic quality reviews
- Presentation and market launch of the Battenberg measurement software RobFlow©
- Market launch of the first Battenberg climate-robotic measuring system
- Founding of Battenberg ROBOTIC GmbH & Co. KG
- Extension of the current company headquarters to include a factory hall
- First use of Battenberg Robotic Measuring in medical technology
- Distribution of Battenberg Robotic Measuring systems worldwide
- First use of the Battenberg Robotic Measuring for lifestyle products
- Extension of the current company headquarters to include a measurement laboratory
- First use of the Battenberg Robotic Measuring in aeronautical engineering
- Market launch of the Battenberg Robotic Measuring for touch panel testing
- Market launch of RobsogPAT measurement optics for automatically finding measurement point coordinates on surfaces
- Market launch of the Battenberg Robotic Measuring for curved touch panel testing and the force feedback function
- Market launch of the Battenberg Robotic Measuring for capacitive display and control devices, testing of touch panels with flat and curved surfaces.
- Standard measurement procedures for pixel accuracy, linearity, jitter, finger seperations and force feedback are already pre-programmed and yet can be freely parameterized.
- The pixel-based coordinate system of the test devices is transferred to the robotic coordinate system in a special calibration process. The pixel coordinates are used to program the RobFlow© robotic measuring software for high-precision measurement and analysis functions.
- Market launch and simultaneous development of FuctionalTwin for virtual robotic measuring:
The FunctionalTwin of the component is a digital functional model that depicts the physical, dynamic functional behavior of the component.
- This makes it possible for the first time in RobSimulation to virtually test virtual, functional components in order to represent virtual test specifications, as well as to program and simulate virtual testing and assembly steps.
- Market launch of RobSimulation for virtual simulation and the real execution of the robotic measuring: RobSimulation visualizes 3-dimensionally, generates virtual robot cells for assembly and quality assurance from CAD data and simulates virtual robot processes long before real components are available.
- The simulation results are transferred directly to real systems at global locations for commissioning. Additional, manual programming work is largely unnecessary.
- As a result of the transfer to global locations, production and quality processes can be standardized and generate significant time and cost advantages.
- Development and implementation with RobSimulation:
The testing of 4 vehicle doors in the entire vehicle.
The multi-robot and the entire test procedures are
Visualized in 3 dimensions, are virtually simulated and tailored to the required test task.
- The optimized simulations are transferred directly to the real multi-robots for virtual commissioning. The vehicle coordinate system is measured into the robot coordinate system via reference points or using a 3D scanner.
- All 4 test processes can then be started immediately with the real vehicle and carried out safely. Manual programming on the vehicle is largely omitted.
- Market launch of RobMobil for robotic measuring robotics (AMR) for functional vehicle validation:
RobMobil is an Autonomous Mobile Robot (AMR) for mobile robotic measuring and robot-assisted assembly tasks in indoor and outdoor areas.
- A 7-axis cobot mounted on the mobile platform, controlled by a real-time location system, drives to the desired target positions in a self-navigating manner. RobMobil processes can be virtually simulated using the RobSimulation software, the CAD data of the measurement object and DigitalTwin.
- The optimized simulation results are transferred directly to the real RobMobil. After the object coordinate system has been calibrated into the cobot coordinate system, the tasks are carried out automatically at the defined 3D measurement points or trajectories.
- With selectable measurement sensors, 3D scanners or robotic tools, RobMobil offers a wide range of applications. For example, in functional vehicle protection, in the QA area of aircraft parts or mobile assembly in production.
- With selectable measurement sensors, 3D scanners or robotic tools, RobMobil offers a wide range of applications. For example, in functional vehicle protection, in the QA area of aircraft parts or mobile assembly in production.

ISO 9001:2015 quality management
By meeting ISO 9001:2015 requirements, we are audited every year to show our customers and business partners that there are suitable processes in our organization to be able to provide high-quality products and services. The required quality of products and services is based on our customer expectations and the relevant legal and regulatory requirements. At the same time, our management system a continuous improvement process.
Reference customers
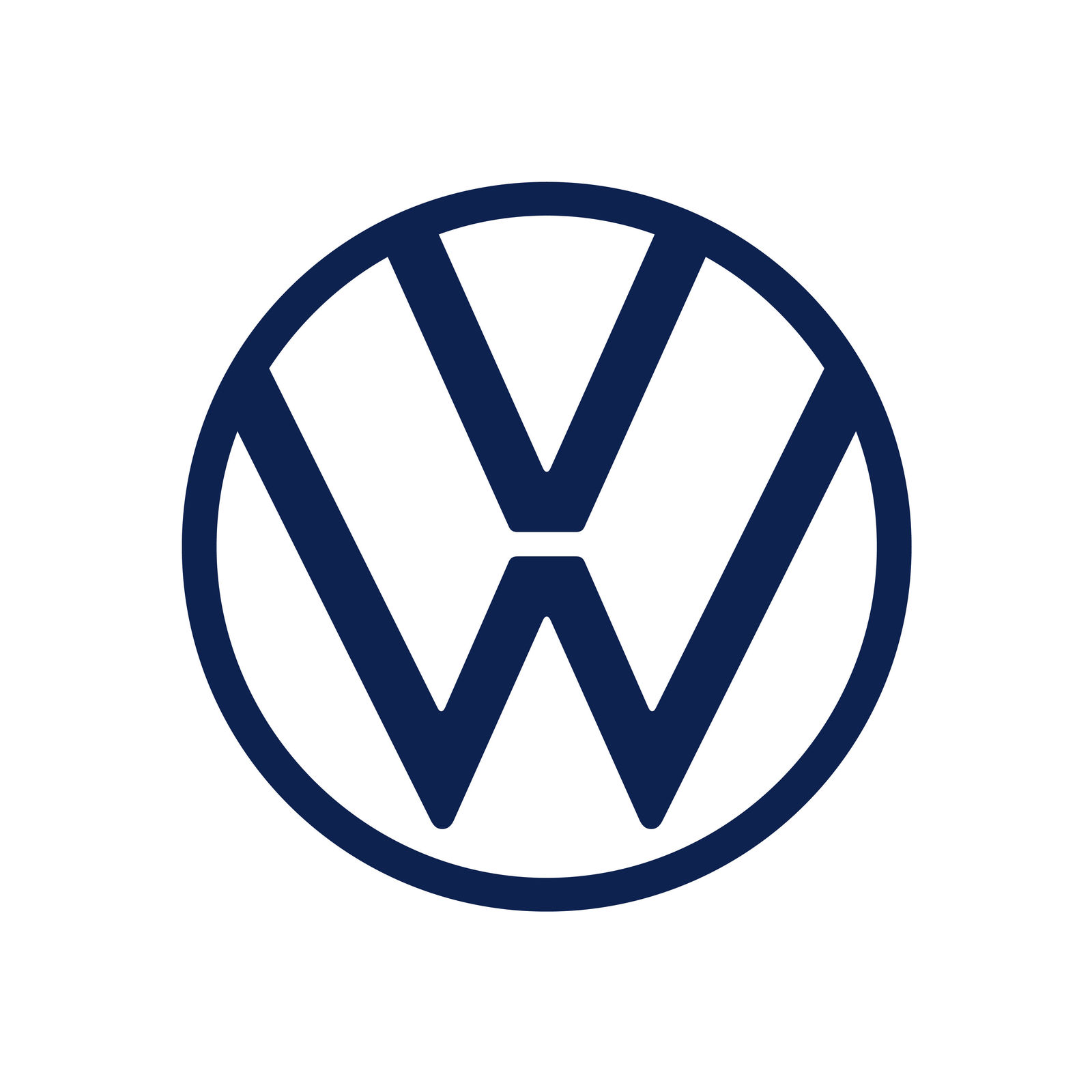
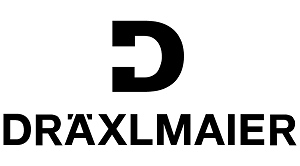
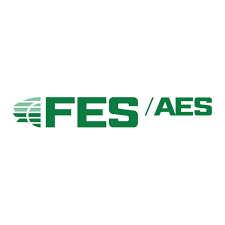
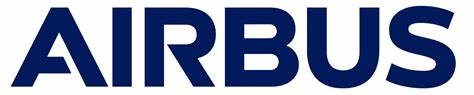

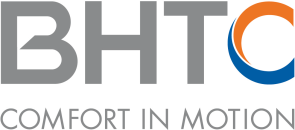
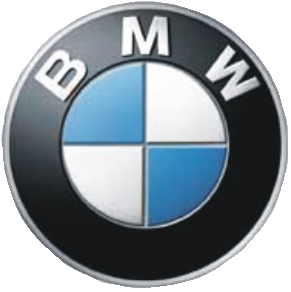
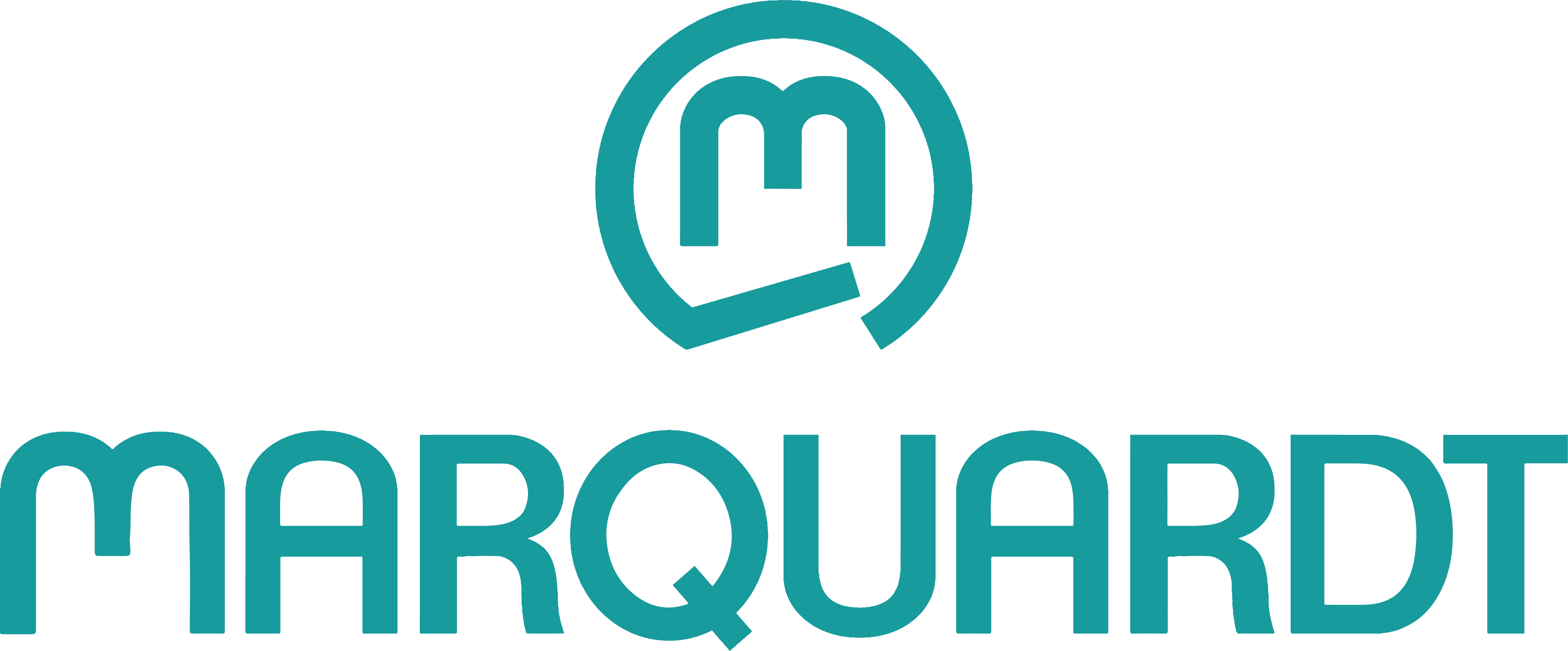
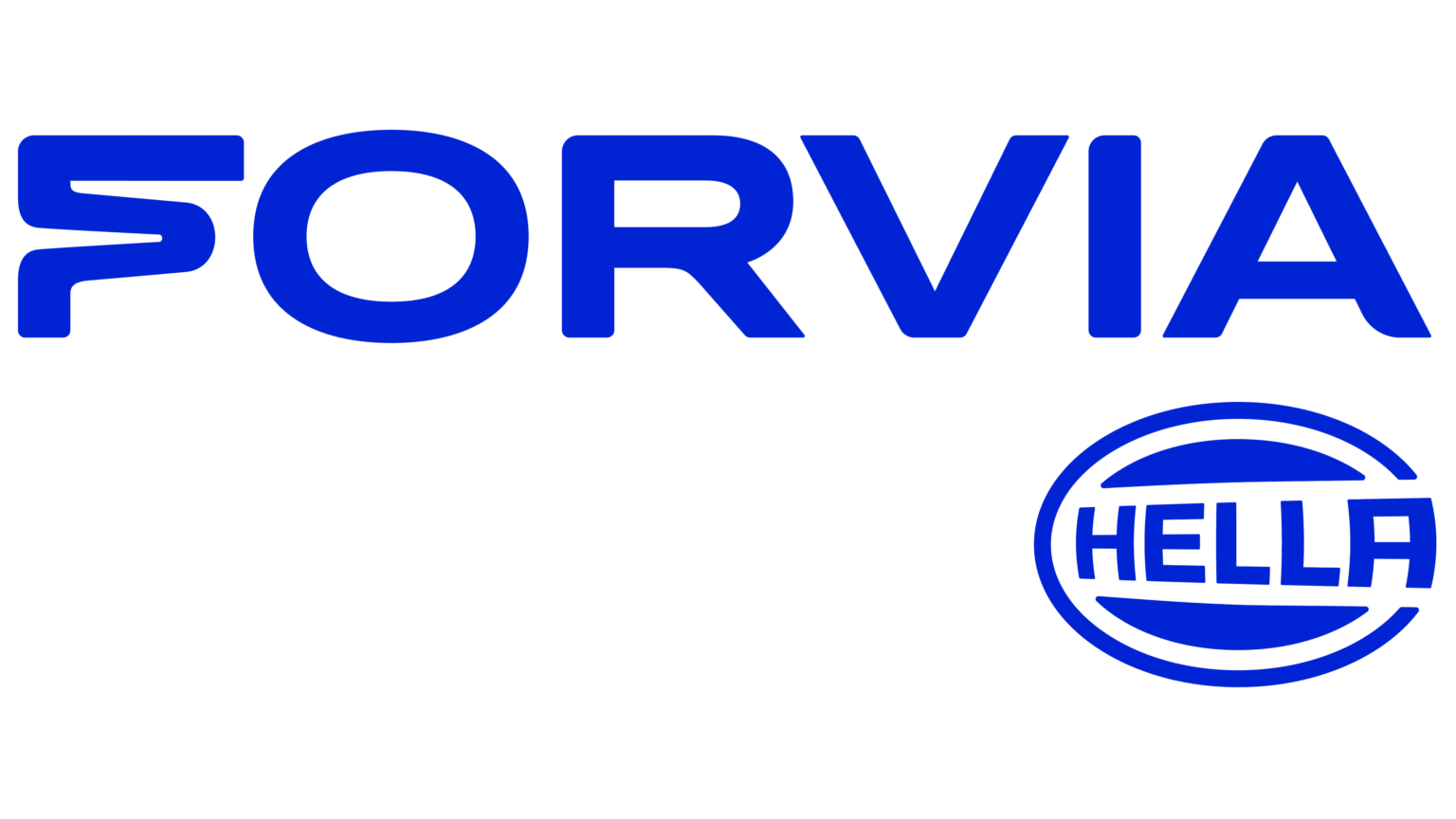
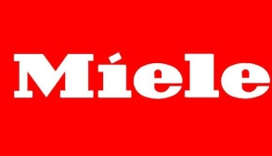
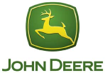
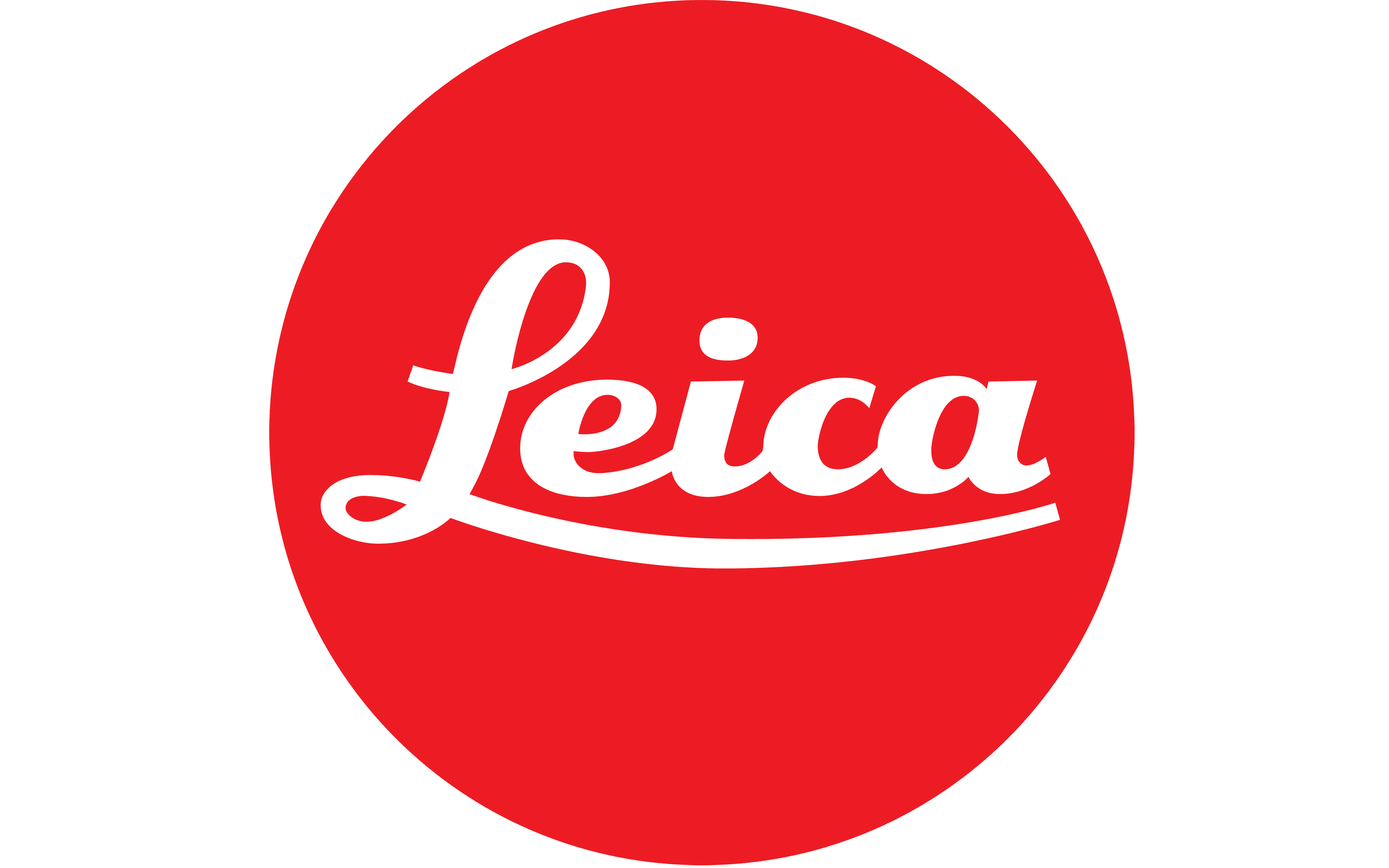


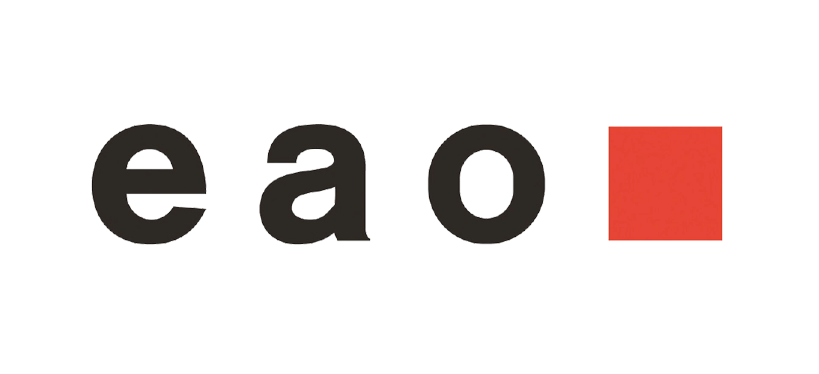
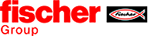
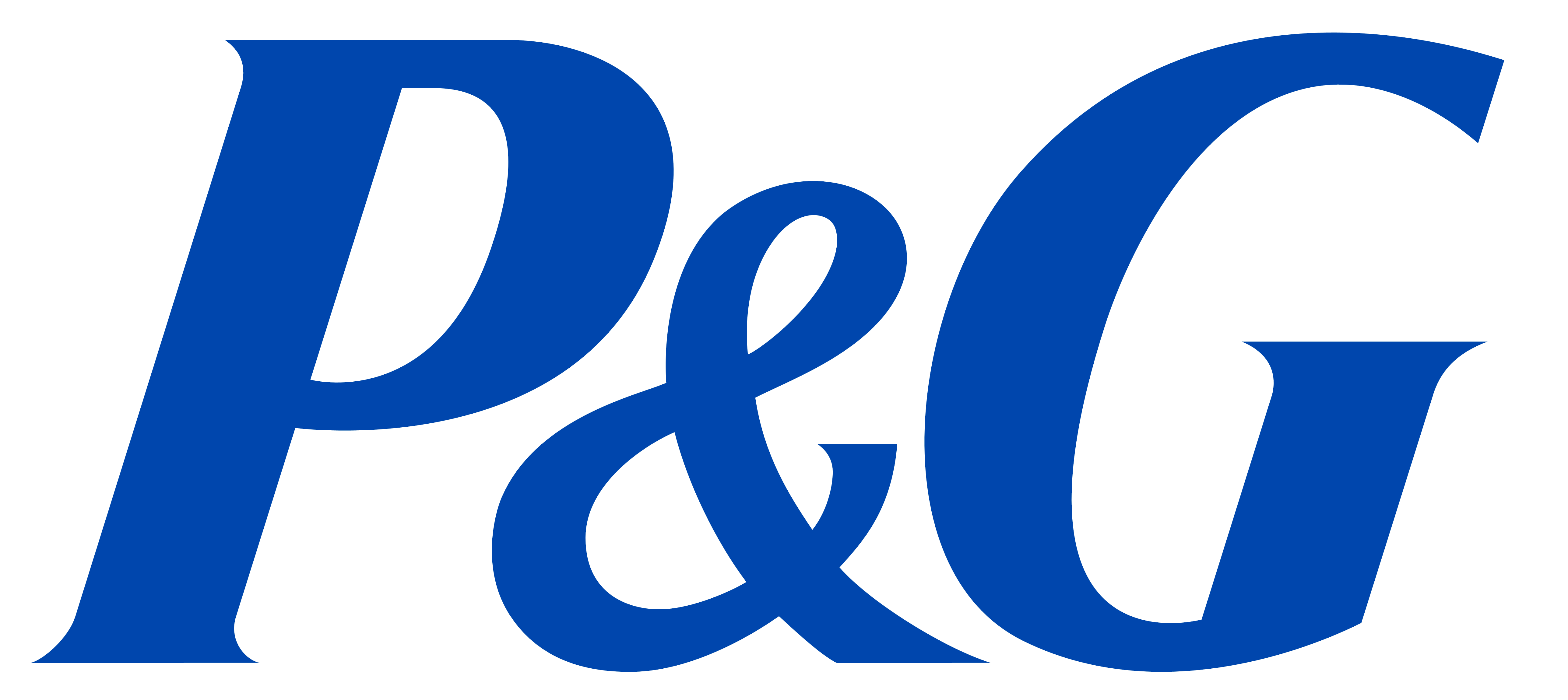

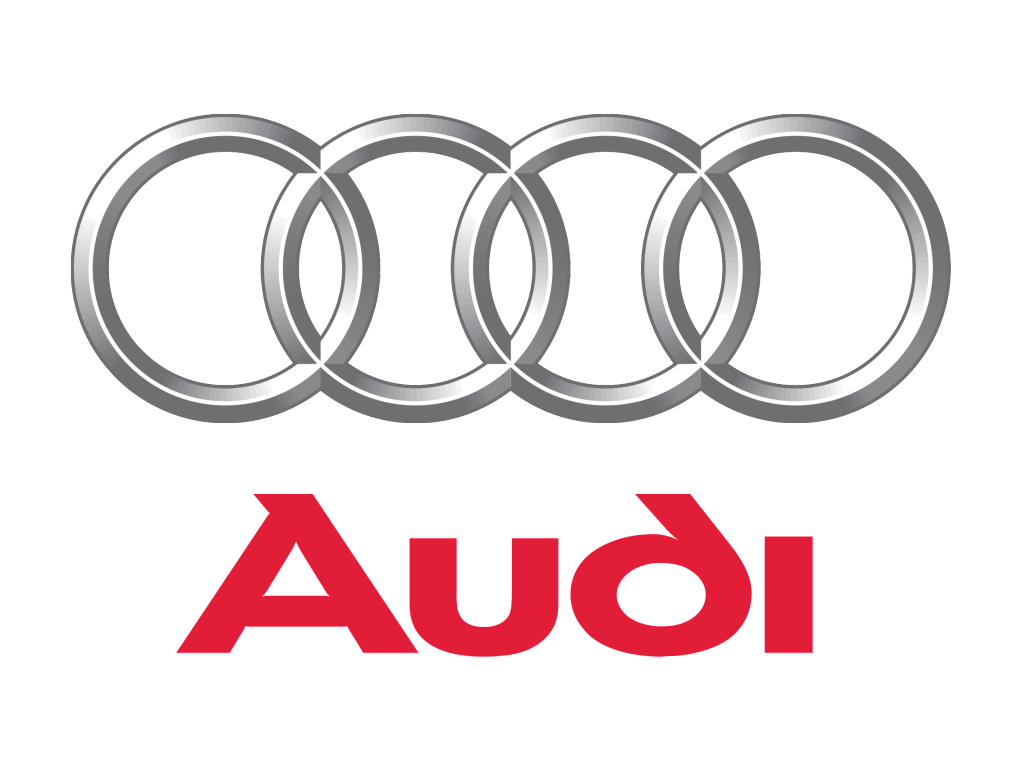
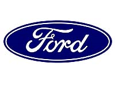
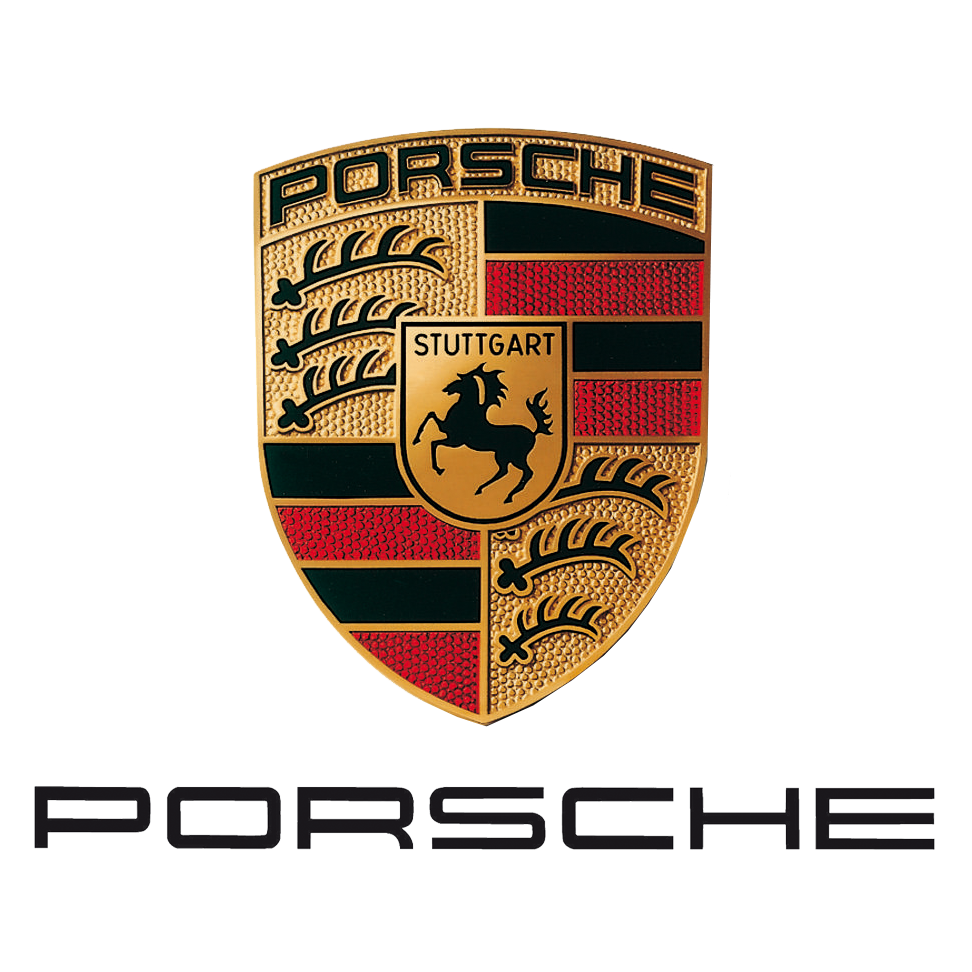
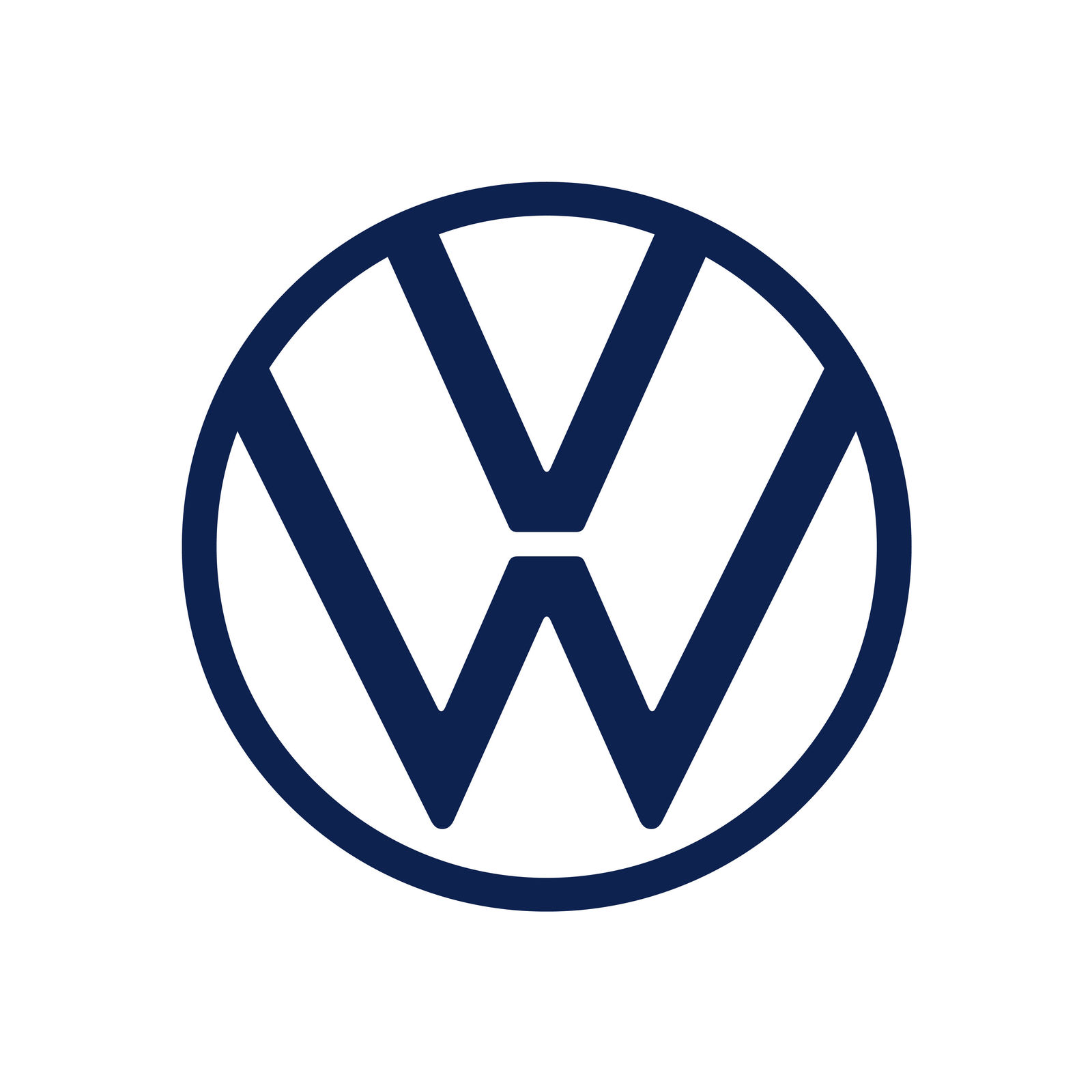
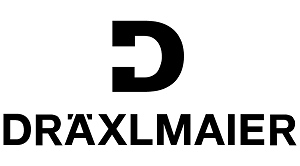
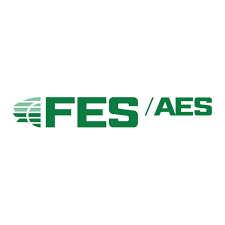
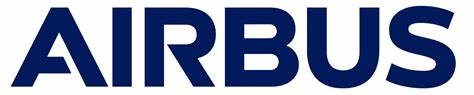


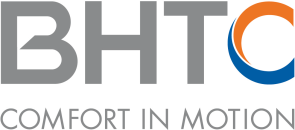
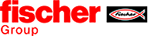
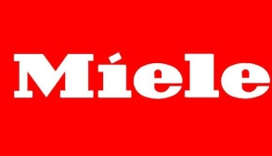
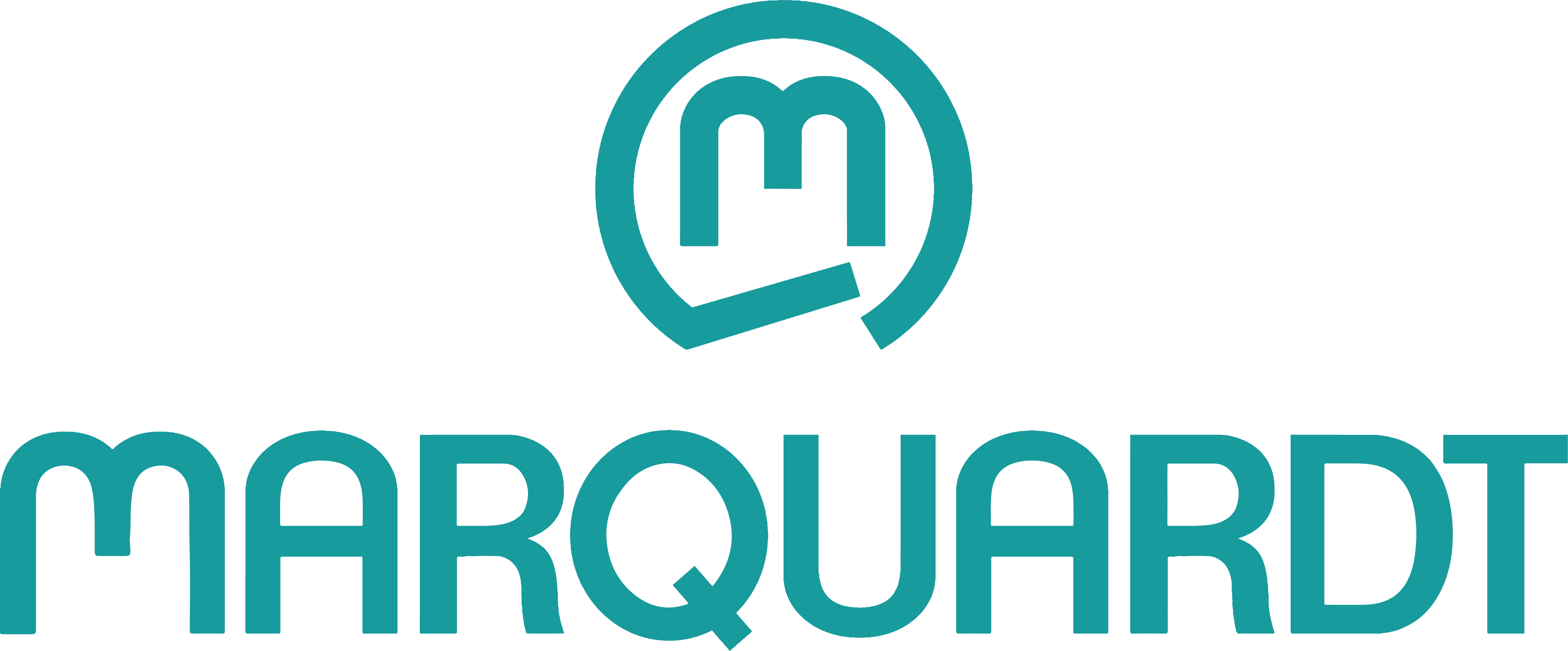
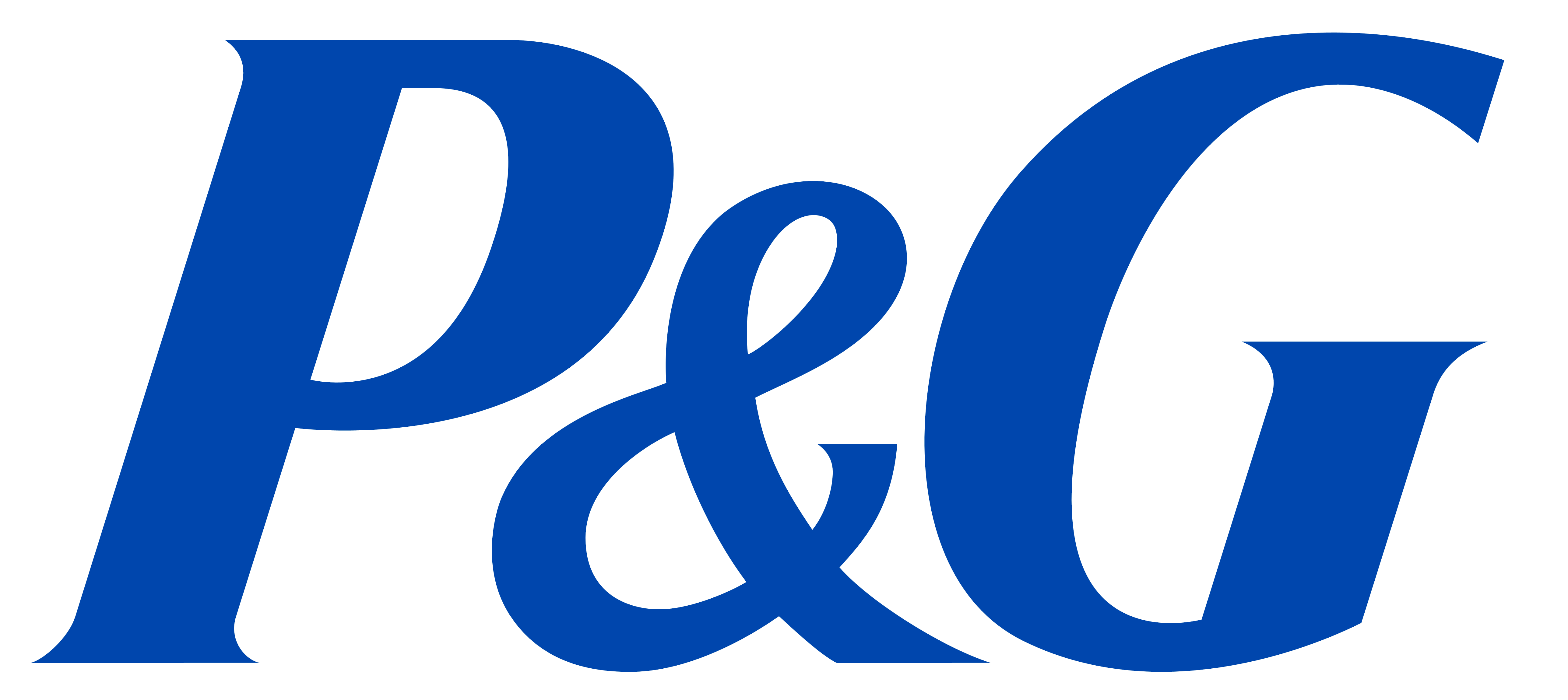
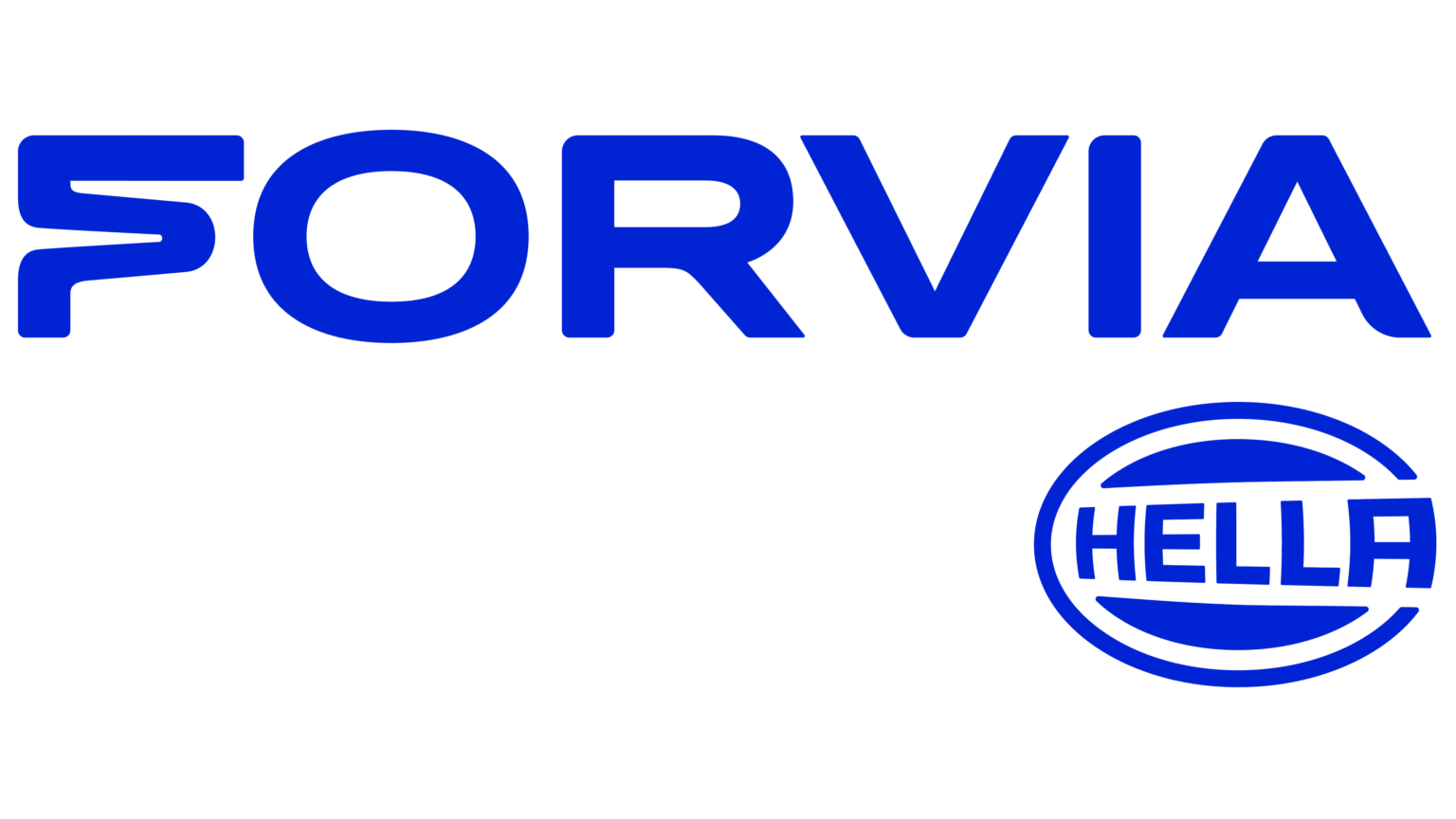
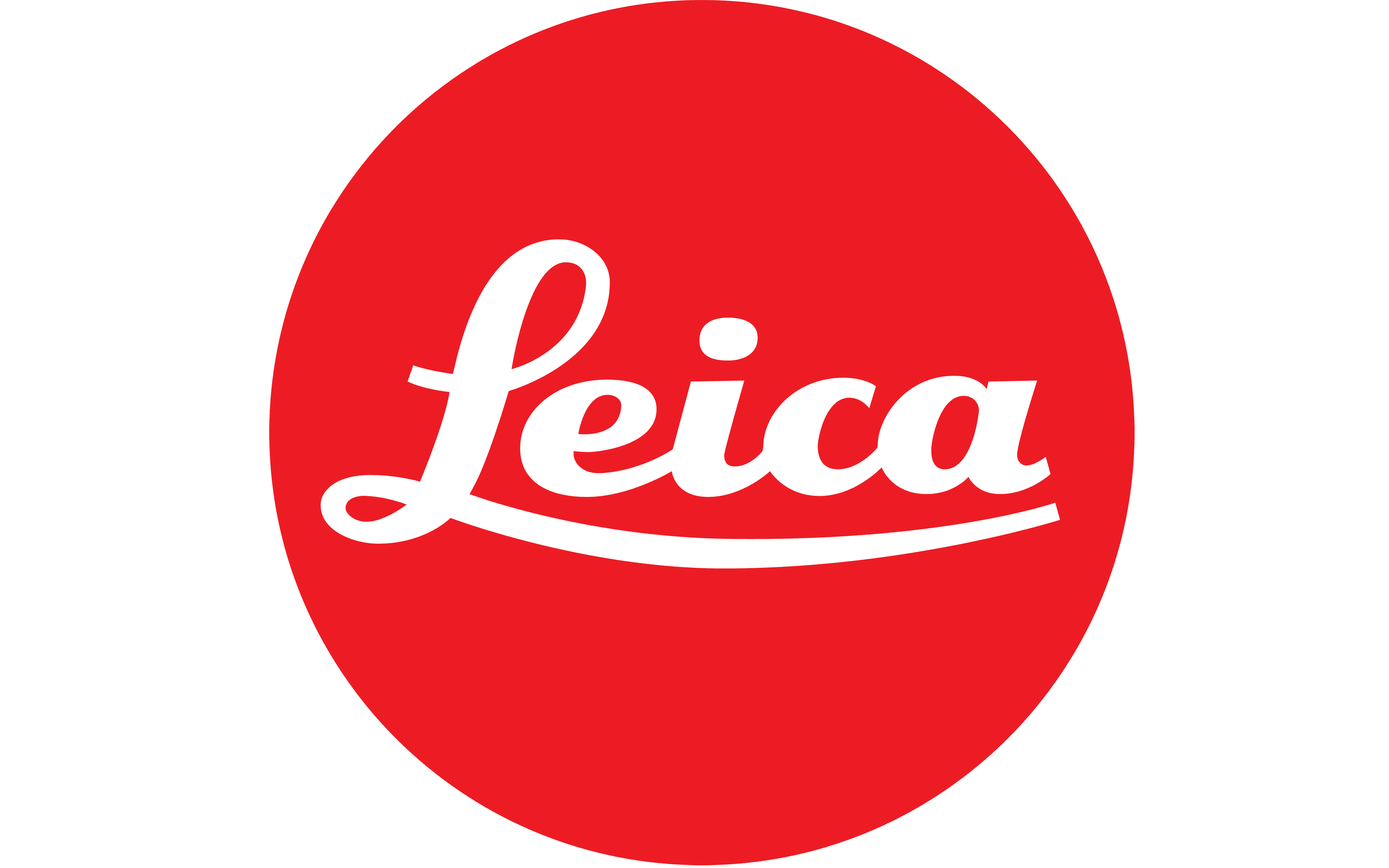
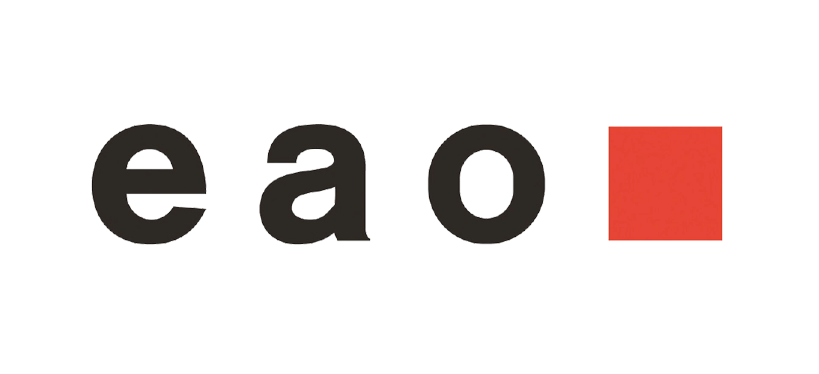
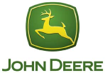

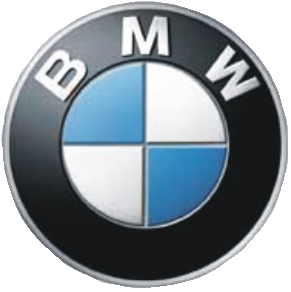

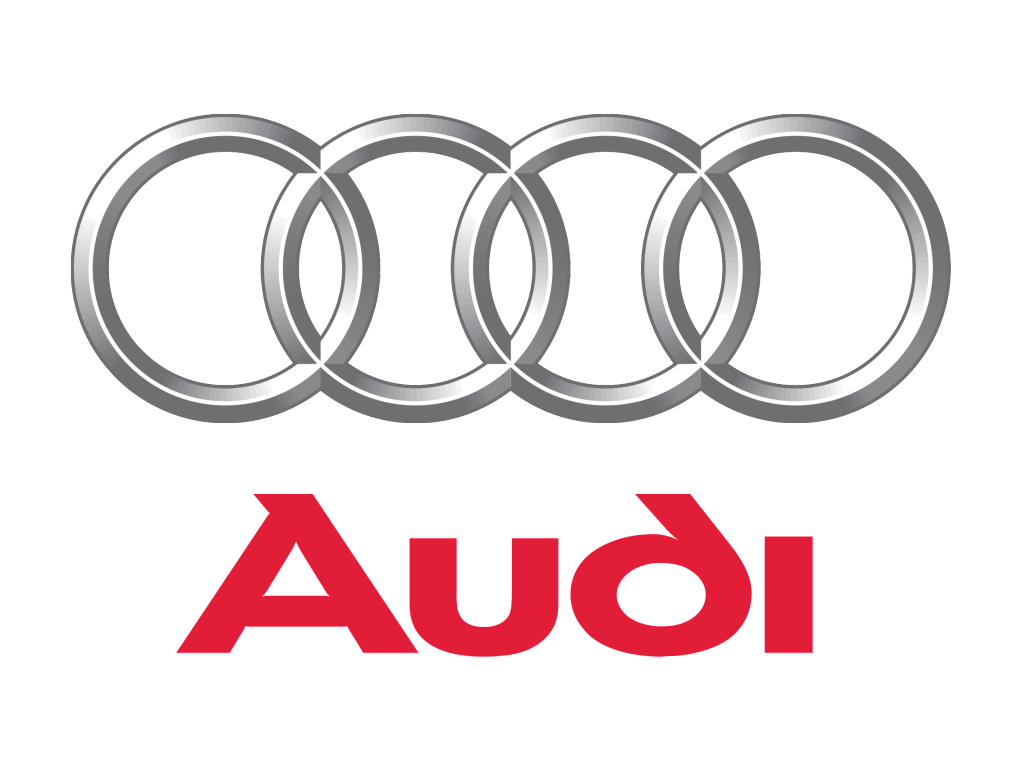
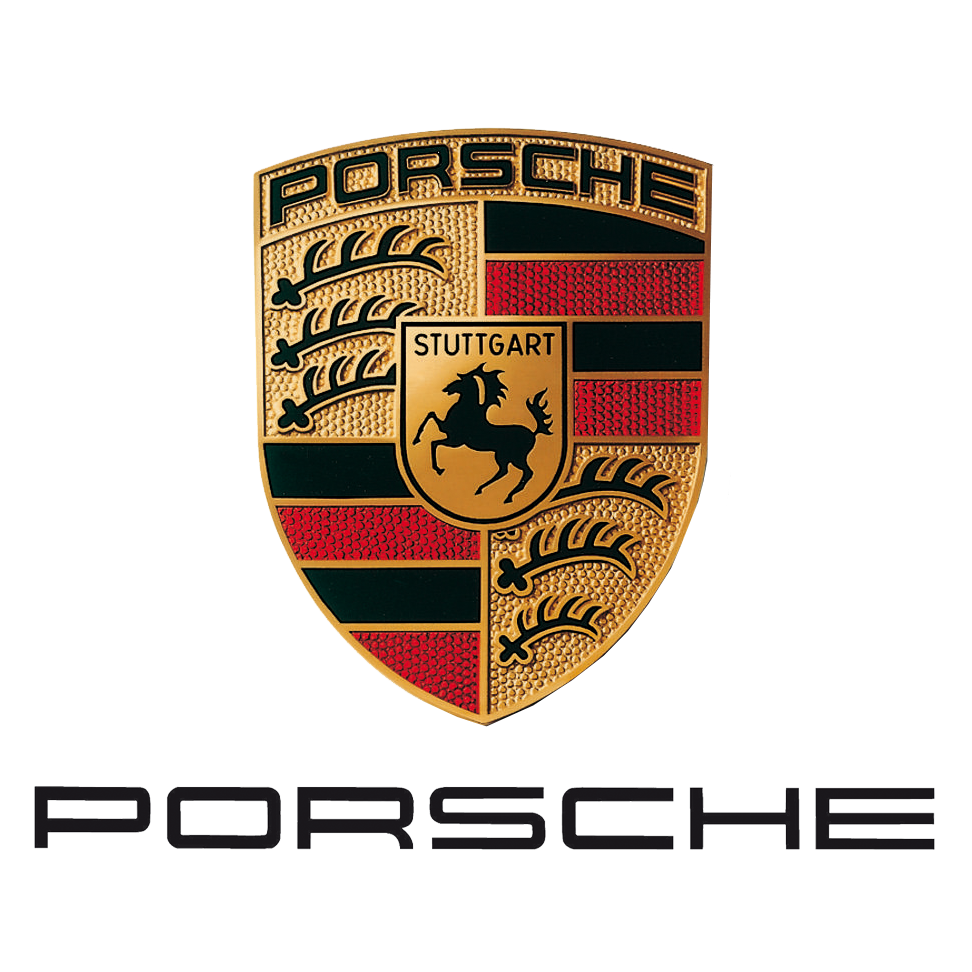
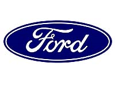